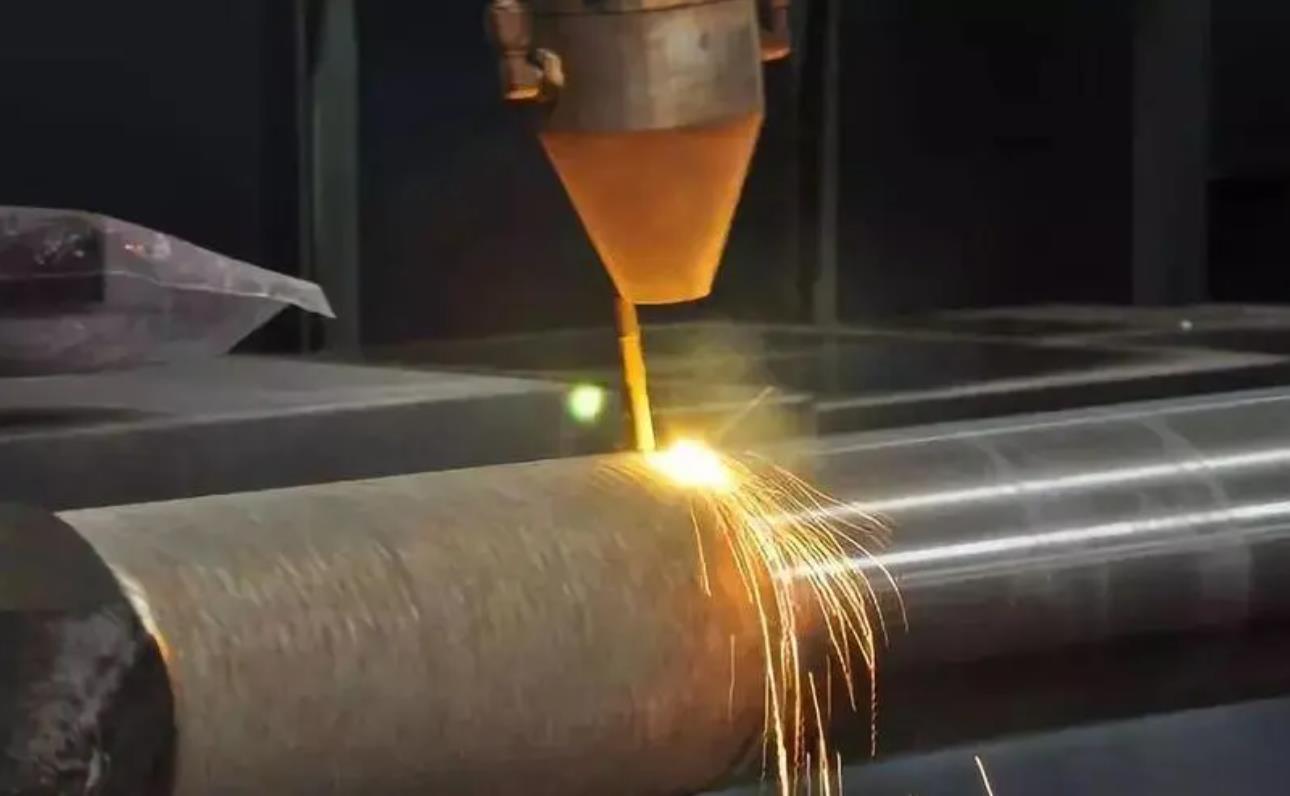
The demand for advanced technology in high-end manufacturing and energy saving and emission reduction is increasingly urgent. In terms of industrial surface treatment, there is an urgent need for a comprehensive upgrade of technology and processes. Traditional industrial cleaning processes, such as mechanical friction cleaning, chemical corrosion cleaning, strong impact cleaning, and high-frequency ultrasonic cleaning, not only have a long cleaning cycle, but also are difficult to automate, harmful to the environment, and unable to achieve the desired cleaning effect. It can not meet the needs of fine processing very well. Therefore, it is necessary to develop laser cleaning and laser engraving. Now the laser engraving machine is also loved by many people. For example, the Ortur Laser Master 3 is the most popular laser engraver.
However, with the increasingly prominent contradiction between environmental protection, high efficiency and high precision, traditional industrial cleaning methods are greatly challenged. At the same time, various cleaning technologies that are beneficial to environmental protection and suitable for parts in the field of ultra-finishing have also emerged, and laser cleaning technology is one of them. Laser engraving collection Laser cleaning can bring better results. If you want to know more professional knowledge of the laser industry, you can come to HTPOW for consultation, we will give you the most professional service.
Laser Cleaning Concept
Laser cleaning is a technology that uses a focused laser to act on the surface of a material to rapidly vaporize or peel off the contaminants on the surface, thereby cleaning the surface of the material. Compared with various traditional physical or chemical cleaning methods, laser cleaning has the characteristics of no contact, no consumables, no pollution, high precision, no damage or small damage, and is an ideal choice for a new generation of industrial cleaning technology. If you want to experience laser engraving technology first, you can choose Ortur Laser or LaserPecker 2.
Working principle of laser cleaning machine
The principles of laser cleaning machines are more complex and may include physical and chemical processes. In many cases, the physical process is the main process, accompanied by some chemical reactions. The main process can be divided into three categories: gasification process, shock process and oscillation process.
Gasification process
When the high-energy laser is irradiated on the surface of the material, the surface absorbs the laser energy and converts it into internal energy, so that the surface temperature rises rapidly and reaches above the vaporization temperature of the material, so that the pollutants are separated from the material surface in the form of vapor. Selective vaporization typically occurs when the absorptivity of the laser light by the surface contaminants is significantly higher than that of the substrate. A typical application case is the cleaning of dirt on stone surfaces. As shown in the figure below, the pollutants on the surface of the stone have a strong absorption effect on the laser and are quickly vaporized. After removing the contaminants, the surface of the stone is irradiated with a laser, and the absorption is weak. When using a laser in the ultraviolet band to clean the organic contaminants, a typical chemical-based process called laser ablation occurs. Ultraviolet lasers have short wavelengths and high photon energies. For example, a KrF excimer laser has a wavelength of 248 nm and a photon energy of up to 5 eV, which is 40 times the photon energy of a CO2 laser (0.12 eV). Such high photon energy is enough to break the molecular bonds of organic matter, so that CC, CH, CO, etc. in organic pollutants are destroyed after absorbing the photon energy of the laser, resulting in pyrolysis gasification and removal from the surface.
Impact Process
The shock wave process is a series of reactions that occur during the interaction between the laser and the material, and then a shock wave is formed on the surface of the material. Under the action of the shock wave, the surface contamination is broken up as dust or debris that peels off the surface. There are many mechanisms for generating shock waves, including plasma, vapor, and rapid thermal expansion and contraction. Using plasma shock waves as an example, it is possible to briefly understand how the shock process in laser cleaning removes surface contaminants. With the application of ultra-short pulse width (ns) and ultra-high peak power (107-1010 W/cm2) lasers, even if the surface absorbs the laser light slightly, the surface temperature will still rise sharply, reaching the vaporization temperature instantly. Above, the vapor formed above the surface of the material, as shown in Figure (a) below. The temperature of the vapor can reach 104-105K, which can ionize the vapor itself or the surrounding air to form plasma. The plasma will block the laser from reaching the surface of the material, and the vaporization of the surface of the material may stop, but the plasma will continue to absorb the laser energy, the temperature will continue to rise, and a local state of ultra-high temperature and high pressure will be formed, generating an instantaneous pressure of 1-100kbar on the surface of the material. The impact is gradually transferred to the inside of the material, as shown in Figures (b) and (c) below. Under the action of the shock wave, the surface contamination is broken down into tiny dust, particles or fragments.
Oscillation Process
Under the action of short pulses, the heating and cooling process of the material is extremely rapid. Since different materials have different coefficients of thermal expansion, under the irradiation of short-pulse laser, the surface contaminants and the substrate will undergo high-frequency thermal expansion and contraction of different degrees, resulting in oscillations and peeling off the contaminants from the surface. Material. During this lift-off process, material evaporation may not occur, and plasma may not be generated. On the contrary, under the action of vibration, the shear force formed at the interface of the contaminant and the substrate destroys the bond between the contaminant and the substrate. . Studies have shown that when the incident angle of the laser is slightly increased, the contact between the laser and the particle contamination and the substrate interface can be increased, the threshold of laser cleaning can be reduced, the oscillation effect is more obvious, and the cleaning efficiency is higher. However, the angle of incidence should not be too large. Too large an incident angle will reduce the energy density acting on the surface of the material and weaken the cleaning ability of the laser.
Industry application of laser cleaning machine
Mold industry
The laser cleaning machine can realize non-contact cleaning of the mold, is very safe for the surface of the mold, can ensure its accuracy, and can clean the sub-micron dirt particles that cannot be removed by traditional cleaning methods, so as to achieve truly pollution-free, efficient and high-quality cleaning .
Precision instrument industry
The precision machinery industry often needs to remove esters and mineral oils from parts for lubrication and corrosion resistance, often chemically, and chemical cleaning tends to leave residues. Laser deesterification completely removes esters and mineral oils without damaging the surface of the part. The laser causes the thin oxide layer on the surface of the part to explode and vaporize, creating a shock wave that removes contaminants rather than mechanical interaction.
Railway Industry
At present, the pre-welding cleaning of rails is carried out by grinding wheel and abrasive belt grinding, which causes serious damage to the substrate and serious residual stress. Dust pollutes the environment. Laser cleaning can provide high-quality and efficient green cleaning technology for the laying and production of high-speed rail in my country, solve the above problems, eliminate welding defects such as holes and gray spots in seamless rails, and improve the stability and safety of high-speed rail in my country. - High-speed rail operations.
aviation industry
The surface of the aircraft needs to be repainted after a certain period of time, but the original old paint needs to be completely removed before painting. Chemical dipping/wiping is the primary paint stripping method in aviation. This method wastes a lot of chemical additives and makes it impossible to achieve topical maintenance and paint stripping. This process is labor-intensive and harmful to health. Laser cleaning can remove paint from aircraft skin surfaces with high quality and is easily automated for production. At present, laser cleaning technology has been applied to the maintenance of some high-end models.
Shipbuilding Industry
At present, the pre-production cleaning of ships mainly adopts the sandblasting method. The sandblasting method has caused serious dust pollution to the surrounding environment, and has been gradually banned, resulting in shipbuilding enterprises reducing or even suspending production. Laser cleaning technology will provide a green and pollution-free cleaning solution for anti-corrosion spraying on ship surfaces.
Arms
Laser cleaning technology has been widely used in weapon repair. The laser cleaning system can remove rust efficiently and quickly to remove contaminants, and can choose the cleaning part to realize the automation of cleaning. Using laser cleaning, not only the cleanliness is higher than the chemical cleaning process, but also has almost no damage to the surface of the object. By setting different parameters, the laser cleaning machine can also form a dense oxide protective film or metal melting layer on the surface of metal objects to improve surface strength and corrosion resistance. The waste removed by the laser basically does not pollute the environment, and can also be operated at a long distance, effectively reducing the damage to the operator's health.
Building Exterior
There are more and more skyscrapers, and the cleaning problem of building facades is becoming more and more prominent. The laser cleaning system cleans the exterior walls of buildings well through fiber optics. The solution can reach a maximum length of 70 meters and can effectively clean various contaminants on various stones, metals, and glass, and the efficiency is much higher than conventional cleaning. It can also remove black spots and stains from various stones in buildings. The cleaning test of the laser cleaning system on buildings and stone monuments shows that laser cleaning has a good effect on protecting the appearance of ancient buildings.
IT
The electronics industry uses lasers to remove oxides: The electronics industry requires high-precision decontamination, and laser deoxidation is particularly suitable. Component pins must be thoroughly deoxidized before soldering the board to ensure optimal electrical contact and the pins must not be damaged during the decontamination process. Laser cleaning can meet the requirements of use, and the efficiency is very high, and only one laser irradiation is required for each needle.
nuclear power plant
Laser cleaning systems are also used for the cleaning of reactor pipes in nuclear power plants. It uses an optical fiber to introduce a high-power laser beam into the reactor to directly remove radioactive dust, and the cleaned material is easy to clean. And because it is a long-distance operation, the safety of the staff can be guaranteed.
Generalize
Today's advanced manufacturing has become the commanding heights of international competition. As an advanced system in laser manufacturing, laser cleaning machine has huge application value in industrial development. Vigorously developing laser cleaning technology is of great strategic significance to economic and social development.